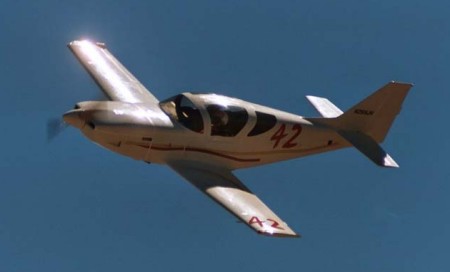
The Glasair was the first kit aircraft that used
moulded surfaces rather than the Rutan method of construction. The
original Glasair 1 required a very long time to construct, but the
newer kits are comparable with other complex kit aircraft. Fast
build options are available. The original company, Stoddard
Hamilton, (named after the late designer) went into liquidation due
to reasons outside the Glasair range. Fortunately the company was
purchased by aircraft enthusiast Thomas W. Wathen and is now going from
strength to strength.
The Glasair is the ideal long distance fast personal
aircraft. These aircraft are not only extremely strong, but fly
better than almost any experimental. They are renowned for their
handling characteristics. In addition, the resins used very rarely
cause allergy problems for builders. The Glasair III is renowned for its performance.
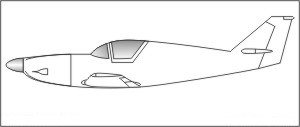
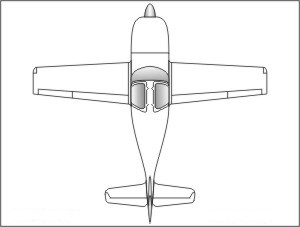
In its evolution from the earliest Glasair models, the III has
grown 30" in overall fuselage length, both forward and aft of
the cockpit. The increased length has given the III markedly
improved longitudinal and directional stability, making it an
impressive platform for serious cross-country and IFR flying.
(The Super II line incorporates these changes as well.)
Since the
Glasair III cruises at speeds up to 313 mph, the factory-moulded
fuselage halves of the III feature incorporate two additional
layers of fibreglass in the outer skin laminates behind the
cockpit to significantly increase the torsional rigidity of
the aft fuselage. Two composite ribs located inside the
vertical fin are bonded to the horizontal stabilizer to
increase stiffness in this area as well.
The belly
section of the III fuselage is stronger and stiffer than that
of the Super II, and it incorporates a strong multiple-screw
and nutplate attachment in the centre section for ease of
removal. The forward belly panel comes with pre-moulded cooling
air exit ramps designed to optimize engine cooling and exhaust
installation for the III’s six-cylinder engine.
The well for
the retractable nose wheel is supplied as a pre-moulded
composite part with high-density foam core inserts moulded in
for attachment of both the nose wheel doors and the rudder
pedals on the inside of the cockpit.
Fire-retardant, closed cell polyurethane foam core is used in
all areas of the III fuselage, including the firewall.
Wing
The Glasair
III’s wing span and area are the same as those of the Super II
-- 23', 3" and 81.3 sq. ft., respectively. However, the lower
aft surface of the LS(1)-0413 airfoil has been modified in the
aileron and flap area on the III to reduce induced drag,
profile drag and trim drag. This change, coupled with the
upswept Hoerner tips, provides light aileron forces even at
higher speeds.
To provide
the additional strength required for the 335 mph redline speed
of the III, extra laminates are moulded into the wing skins and
spars. In addition, the main spar attach fittings and the wing
attach support brackets on the fuselage are larger than their
counterparts on the Super II, and the composite airframe
structure around the wing attach points has received extra
reinforcement.
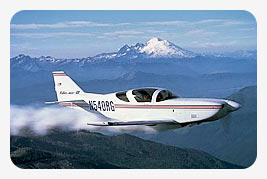
The Glasair
III wing features pre-moulded main landing gear support boxes.
These rigid, structural boxes eliminate the majority of the
laminating and jigging work on the main landing gear
installation and simplify the job considerably.
Control
Surfaces
The Glasair
III uses the same horizontal stabilizer airfoil section as the
Super II. However, graphite fibers have been incorporated into
the skin laminates of the III stabilizer and the span has been
shortened compared to the Super II to obtain the higher degree
of stiffness and torsional rigidity prescribed by our in-depth
vibration testing and computer flutter analysis.
The III also
features larger-diameter aluminium push-pull tubes for the
aileron and elevator control systems than earlier Glasair
models, providing increased column load capacity. Increased
mechanical advantage is provided in the flap control system,
which has been designed to reduce the effort required for flap
actuation while maintaining a simple manual linkage.
Electrically actuated flaps, both standard and slotted, are
available as options.
Landing
Gear
Durable
oleo-pneumatic landing gear struts are used for all three
wheels on the Glasair III. These are top quality, rugged and
designed with low-maintenance features throughout. Internal
fluid metering has been customized for the Glasair’s weight to
give smooth taxiing over rough ground, as well as proper
damping for hard landings. The internal parts are designed so
that specialized wrenches are not required for disassembly,
and service can, if necessary, be accomplished by a novice
with the detailed service instructions New Glasair LLC - New
GlaStar LLC provides.
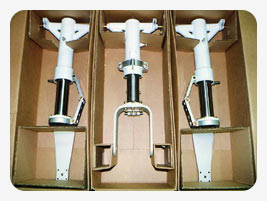
The landing
gear is retracted by an electro-hydraulic pump driving
actuating cylinders. The complete retraction cycle takes about
ten seconds. The gear is controlled by a switch on the
instrument panel and monitored with a panel-mounted hydraulic
pressure gauge and three gear position lights. The lights
indicate gear down and locked (green), gear in transit (red),
and gear up and locked (lights out). Additionally, a warning
horn is activated if the flaps are lowered prior to gear
extension.
The III also
features a gear up-lock system, which is essential for any
high-performance retractable-gear airplane, especially one
that may be subjected to high-G, aerobatic manoeuvring. The
up-locks release automatically when the hydraulic actuators
begin their cycle.
Another
standard system on the III is a cockpit-operated, manual
system for emergency gear extension -- obviously an important
safety feature. The system, which utilizes a hand pump and
special single-direction actuators, is completely separate
from the main hydraulic system, providing true redundancy in
the event of a malfunction.
The massive
oleo nose gear installation mates to the engine mount in a
simple, bolt-on operation. The strut features a heavy-duty
machined shimmy damper collar, which is important for high
speed taxiing. The nose wheel of the III -- like all
tricycle-geared Glasairs -- is free-castoring. Steering on the
ground is accomplished with differential braking at very slow
speeds and using the remarkably effective rudder at higher
taxi and take-off speeds.
The landing
gear also features a powerful braking system including master
cylinders, reservoir, aluminium tubing brake lines, fittings
and heavy-duty brakes. These brakes use 3/8"-thick discs,
which provide better heat dissipation and permit higher piston
forces on the pads than standard, 5.00 x 5 brakes.
Cowling
The Glasair
III cowling has been optimized to provide outstanding engine
cooling with minimal aerodynamic drag. The protruding exhaust
tunnel common on other Glasair models has been eliminated on
the III in favor of twin exhaust stacks that protrude only
slightly beyond the cowling. This change greatly reduces drag
by allowing for a sleek, uninterrupted belly contour from
spinner tip to tail.
The III
cowling is manufactured with extra stiffness because of the
airplane’s high-speed capability. The cowling halves are made
exclusively with special fire-retardant resin and foam core
materials.
The oil
access door is factory-moulded and ready to install into a
moulded inset in the upper cowling. A flush-fit landing light
lens sized to fit a moulded recess in the lower cowling is also
a standard kit feature.
Engine
The Glasair
III uses a certified Lycoming aircraft engine. With such
exciting cross-country capabilities, having a proven, reliable
engine is a must.
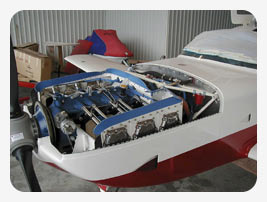
The
Glasair III is designed to use the most readily available 300
hp Lycoming engine, the IO-540-K series. The engine installed
in our prototype III is a smooth-operating -K1H5. This engine
has the fuel injector mounted on a straight air inlet housing
on the aft side of the engine oil sump. It is equipped with a
Bendix RSA-10ED1 fuel injector, a diaphragm-type fuel pump and
drive, and two impulse coupling magnetos.
The
IO-540-K1H5 engine can be purchased new direct from New
Glasair LLC - New GlaStar LLC at an attractive, original
equipment manufacturer’s (OEM) price, but this engine is
unlikely to be found on the used or overhauled market, since
it is not used on any production aircraft. Several 300 hp
IO-540 models that do show up frequently for sale can be used
in the III, however.
The factor
that determines which models can easily be used is the engine
induction system. Induction air in the III is routed from a
NACA duct on the left side of the cowling through a full-time
air filter connected to the injector body by a moulded flex
coupling. The injector is mounted sideways in the cowling on a
90° steel elbow (supplied in the standard kit) that fits onto
the engine’s air inlet housing. In order to obtain the proper
firewall and engine mount clearance for this induction system,
a straight (rather than angled) air inlet housing must be used
on the rear of the oil sump.
Because they
were used in the Piper Cherokee Six, the 300 hp IO-540-K1A5
and -K1A5D (with impulse coupling magnetos) are widely
available as used engines and would be good choices for the
Glasair III. These engines used aft-mounted, 38-1/2° offset
air inlet housings instead of the required straight housing,
but exchanging housings is a simple and relatively inexpensive
operation.
Note: The
common fuel pump on the Cherokees was the smaller but very
expensive Lear-Romec style.
The 300 hp
IO-540-K1E5, used on the Bellanca Viking, is also readily
available used. It comes with the straight air inlet housing,
Lear-Romec fuel pump, and Bendix RS-type fuel injector. This
style of Bendix injector, unfortunately, is not optimal for
use in the Glasair III. If you want to use this engine, we
recommend exchanging the RS injector for an RSA-10ED1
injector.
Note:
Many other models of the Lycoming IO-540 can be modified for
use in the Glasair III. If you find a great deal on an engine
not discussed above, call our Builder Support Department for
advice.
Propeller
Both
80"-diameter Hartzell and 79"-diameter McCauley Blackmack
two-bladed, compact-hub constant-speed propellers can be used
on the Glasair III. After extensive testing, two-bladed props
were selected over three-bladed models due to their
efficiency, lighter weight and lower cost. The landing gear
legs are sized to give a healthy 10" of ground clearance with
either of these props.
The prop is
not included in the kit, but a complete spinner installation
is standard. The composite spinner is manufactured to
perfectly match the loft lines of the Glasair cowling.
Hartzell and McCauley propellers are available, factory-new,
at OEM prices direct from New Glasair LLC - New GlaStar LLC.
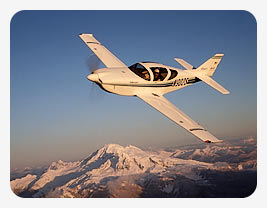
specifications
powerplant
propeller
length
height
wing span
wing area
seats
empty weight
useful load
gross weight
fuel capacity
range |
300 h.p.
x
21.3 ft
7.5 ft
23.3 ft
81.3 sq ft
2
x
x
2,400 lbs
65 gal
8 gal header Tank
11 gal
Wing Tip Extensions
1100 |
performance
takeoff distance,
ground roll
rate of climb
max speed
cruise speed
landing distance, ground roll
service ceiling |
x
2990 ft/min
260 knots
272 knots (turbo)
x
30,000+ ft.
Turbocharged |
limiting and recommended speeds
design manoeuvring speed (Va)
never exceed speed (Vne)
stall, power off (Vsl)
landing approach speed |
174 knots
291 knots
69 knots
x |
All specifications are based on manufacturer's
calculations |